Many companies look to industry leaders to understand how they solve the ever-changing challenges of Supply Chain management. John Kern, Senior Vice President, Supply Chain Operations at Cisco recently explained …
Many companies look to industry leaders to understand how they solve the ever-changing challenges of Supply Chain management. John Kern, Senior Vice President, Supply Chain Operations at Cisco recently explained Cisco’s experience of replacing their core operating software including their ERP, Supply Chain Management software, Data Management and Analytics. Most importantly, this marked a bold step into the conceptual “Internet of Everything.”
Cisco Supply Chain operations manages over 30,000 orderable items and ships over 4,700 orders daily to every corner of the globe. This change in technology and operations marked a major undertaking.
Like most Supply Chain projects Cisco’s focus was on improving:
- Overall quality in operations
- Cost
- Delivery
- Management of new product introductions
Cisco was looking for measurable improvements in:
- Lower delivered costs
- Faster response times
- Meeting rising customer service expectations
- Management of more customized products & services
- Management of volatility of demand
- The number of products
- Increasing volatility of supply
- Smaller, more frequent shipments
- Supply chain transparency
One of the key segments of the Cisco project was Distributed Order Management. A recent trend has been identified in that many companies seeking the same measurable objectives which is to install Distributed Order Management – DOM. Originally many of these organizations acquired the use of DOM as a powerful tactical tool tasked with efficiently managing order flow. In line with their original objectives, they achieved improved distribution cost savings including lower per unit costs in transportation and packaging. They also realized measured improvements in customer service including on-time shipping and order fulfillment.
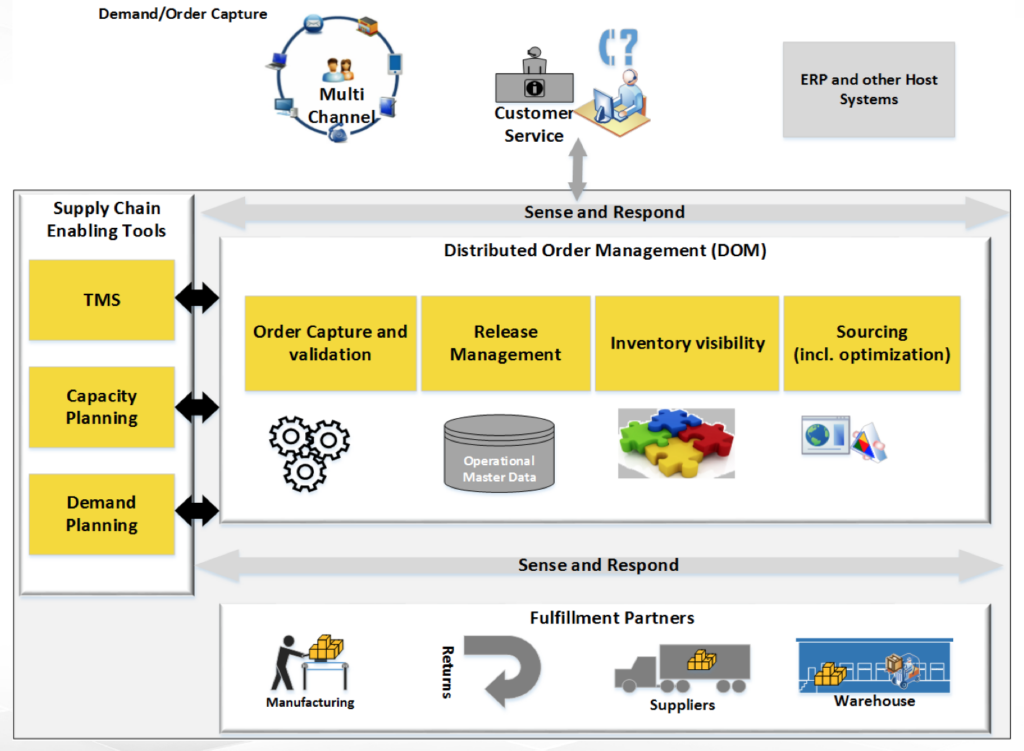
Through these early successes these companies recognized DOM offered improved analytics. In their constant quest for improvement through people, process and technology, DOM became a new window to business data generated by the flow of inventory and orders. Users set up new measurements such as:
The number of orders transferred per site per month
- The number of orders affected by early or late seasonality
- The number of rush shipments per shipping location
- The number of drop ships
- Substitutions data
- Changes required to meet Country of Origin requirements
- Data related to Forward Deployed Inventory
- Order transfers to achieve same-day shipping
- Inventory turnover ratios by inventory sku and/or type or group
- Cost per product shipped and/or order shipped
- More unique to each business operation
Analytics captured and presented on a continual real-time basis identify important trends and contribute to executive decisions such as:
- regional, national and global inventory placement and shipment strategies
- vendor ship, store, factory, & centralized ship strategies, and other geographic business decisions
- energy use plans
- customer service programs
- Passing meaningful data to other systems through Cloud technology
DOM delivered with Cloud technology offers that first bold step into the Internet of Everything. It provides the opportunity to connect with “the unconnected” and share data with other systems not previously possible. As a result, the change in IT affects the thought and capability of Operation Technology (OT) not previously known within your organization. The result in greater collaboration internally and externally with business partners and customers.
Locally or globally, Softeon DOM can provide real time order and inventory analytics critical to optimum asset performance and customer service.